Understanding Six Sigma Projects: A Comprehensive Guide
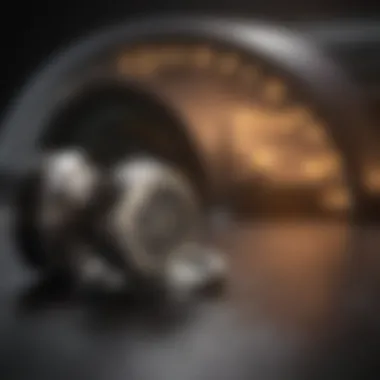
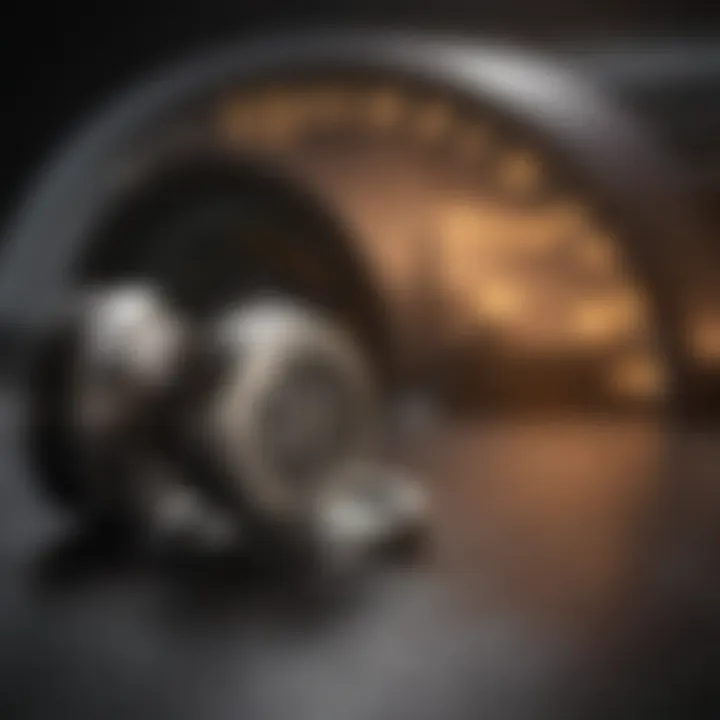
Intro
In the quest for excellence, organizations across diverse industries are continuously seeking ways to enhance their operations. The Six Sigma approach, with its goal of minimizing defects and maximizing quality, stands out as a reliable methodology. Rooted in data-driven decision-making, Six Sigma not only challenges the status quo but also encourages a systematic examination of processes. By understanding this framework, you unlock doors to efficiency and effectiveness that can transform how businesses operate.
This guide offers a comprehensive insight into Six Sigma projects, delving into the pivotal principles, methodologies, and the significant role project management plays within this domain.
Whether you are a seasoned professional or just dipping your toes into the waters of Six Sigma, you'll find this narrative both enlightening and practical. From discussing key tools and techniques to showcasing real-world applications and case studies, this guide paints a holistic picture of how Six Sigma can boost performance in various sectors.
As we embark on this journey, prepare to uncover not just strategies, but also the critical thinking that underpins successful Six Sigma projects.
Preamble to Six Sigma Projects
Understanding the concept of Six Sigma projects gives one a formidable toolset aimed at enhancing quality and efficiency in various domains. In todayās fast-paced business landscape, optimizing processes and minimizing errors have become vital for maintaining a competitive edge. By implementing Six Sigma strategies, organizations can systematically tackle inefficiencies and elevate customer satisfaction to new heights. This kind of systematic improvement not only curtails waste but also aligns operations with customer requirements.
When we speak of Six Sigma, we are referring to a disciplined, data-driven approach that leverages statistical methods to eliminate defects in any process. The worth of Six Sigma projects lies in their potential to deliver remarkable improvements and promote a culture of accountability, thereby fostering an environment where all employees can contribute to a companyās success. It's not just about numbers; itās fundamentally about enhancing the experience for the end-user or customer.
Definition and Purpose
Six Sigma can be understood as both a methodology for quality improvement and a set of techniques for its implementation. At its core, the term "Sigma" is a statistical representation that signifies standard deviation from the mean. The goal of Six Sigma is to minimize variation and reduce defects to a statistically significant level, specifically aiming for no more than 3.4 defects per million opportunities. This ambitious target epitomizes excellence in process excellence, which many organizations strive to achieve.
The purpose of Six Sigma initiatives extends beyond mere defect reduction. Companies often embark on Six Sigma projects to:
- Enhance Customer Satisfaction: A focus on quality directly translates into higher customer loyalty and business credibility.
- Reduce Costs: Streamlining processes leads to cost reductions without sacrificing quality.
- Foster a Culture of Continuous Improvement: The methodology instills a mindset that values ongoing assessment and enhancement of processes.
- Drive Data-Driven Decisions: Six Sigma hinges on making decisions based on solid data rather than mere intuition.
Historical Context
The roots of Six Sigma can be traced back to the mid-20th century, chiefly attributed to the manufacturing industry. The methodology gained prominence in the 1980s at Motorola, where it was first implemented as a robust framework for quality management. The groundbreaking leadership of Bill Smith, who is often referred to as the father of Six Sigma, laid the groundwork for its wide adoption.
From the manufacturing floors, Six Sigma gradually seeped into diverse sectors ranging from healthcare to finance. Companies like General Electric propelled its popularity throughout the 1990s, realizing staggering improvements, which inevitably attracted global attention. This cross-industry appeal underscored how Six Sigmaās principles could apply universally, making it a versatile approach for various organizational challenges.
In summary, the introduction to Six Sigma projects reveals not just its significance as a methodology but also its transformative potential across industries. As businesses grapple with the challenges of modern-day operations, the principles of Six Sigma emerge as a beacon of hope, unveiling pathways to substantial improvement and customer-centric strategies.
Key Principles of Six Sigma
Six Sigma stands as a robust methodology aimed at improving processes, curtailing defects, and enhancing overall quality. The key principles underpinning Six Sigma are pivotal, not only for grasping its methodologies but also for realizing its profound impact on organizational performance. By leveraging these principles, organizations can translate their aspirations for efficiency into actionable strategies.
Customer Focus
At the heart of Six Sigma lies a resolute commitment to customer satisfaction. This principle prioritizes understanding the needs and expectations of customers, which is crucial in todayās competitive landscape. Companies are not merely incentivized to deliver products and services; they must do so in a way that aligns with customer desires.
By adopting a customer-centric approach, businesses can identify the critical-to-quality (CTQ) elements that matter most to their clientele. This involves employing various methods such as surveys or feedback loops to capture customer insights. Consequently, when organizations design their processes around the voice of the customer, they stand a greater chance of exceeding expectations and fostering loyalty.
"When you put the customer first, all else becomes secondary."
Data-Driven Decision Making
In the dynamic realm where Six Sigma thrives, data isn't just importantāit's everything. Data-driven decision making encapsulates the essence of analytics within this framework. Six Sigma practitioners rigorously collect and analyze data to unveil the reasons behind problems or defects. Relying on empirical evidence facilitates informed choices, steering clear of guesswork or assumptions that could derail project success.
Organizations often deploy statistical tools to interpret this data, guiding them in identifying patterns or anomalies that require attention. For instance, a production line experiencing higher defect rates can benefit immensely from data analysis, pinpointing the exact causes. This not only enhances the quality of the outputs but also aids in optimizing resource allocation.
Process Improvement
The ultimate objective of Six Sigma is to refine processes to enhance quality, reduce waste, and increase efficiency. Process improvement revolves around identifying existing flaws in workflows and implementing systematic changes. This isnāt a mere tweak here and there; itās an overhaul grounded in analysis and precise execution.
Utilizing methodologies such as DMAIC (Define, Measure, Analyze, Improve, Control) helps teams systematically approach process enhancement. In essence, organizations embark on a journey of continuous improvement, which is crucial for sustaining competitive advantage in a fast-evolving market. Achieving process improvement reshapes not only the operational efficiency but also the organizationās culture, embedding a mindset of constant enhancement across all levels.
- Key elements of process improvement include:
- Identifying inefficiencies
- Redesigning workflows
- Engaging stakeholders
- Implementing control measures
This comprehensive focus on process refinement leads to tangible outcomes, driving success and fostering innovation within the organization.
Six Sigma Methodologies
Six Sigma methodologies serve as the backbone of the holistic approach that defines Six Sigma projects. By leveraging distinct frameworks tailored to specific types of projectsānamely DMAIC and DMADVāorganizations can systematically tackle inefficiencies and elevate their operational standards. The significance of these methodologies lies in their structured yet flexible nature, which allows teams to adapt them to their unique contexts and challenges. Each methodology brings its own set of tools and principles that can transform processes, reduce defects, and ultimately drive profitability.
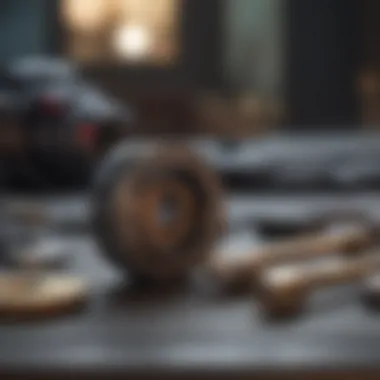
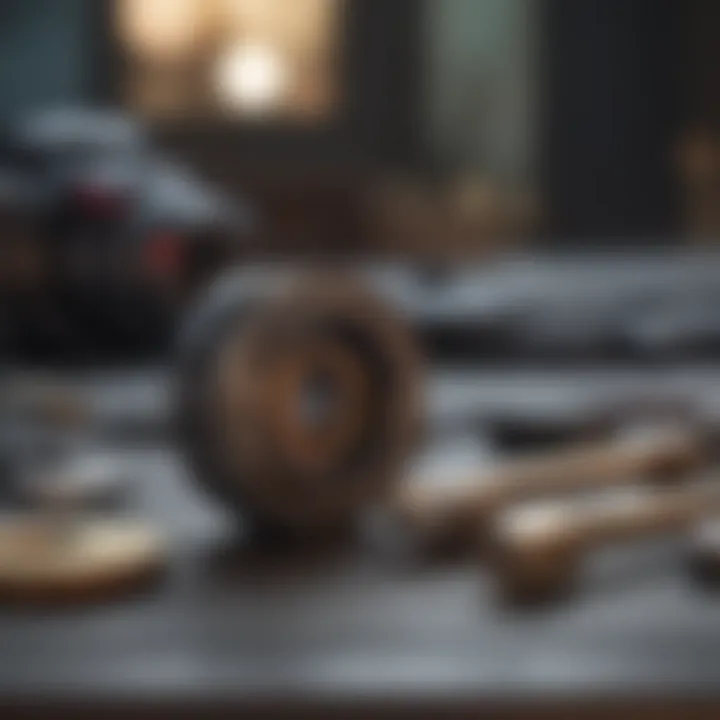
DMAIC Framework
The DMAIC frameworkāstanding for Define, Measure, Analyze, Improve, and Controlāis the cornerstone of Six Sigma project execution. Its structured approach ensures that every critical aspect of a project is meticulously addressed.
- Define: This initial phase requires the team to outline the problem and set clear, measurable objectives. For example, a manufacturing company might identify that a specific product line is consistently falling short of quality standards.
- Measure: In this phase, relevant data is collected to understand current performance levels. This often means diving into production metrics or customer feedback to quantify defects.
- Analyze: Here, the real detective work happens. The team investigates the data, looking for root causes of issues. Utilizing tools like Pareto diagrams or fishbone charts can illuminate underlying problems.
- Improve: Once root causes are pinpointed, creative solutions are brainstormed and trialed. This stage revolves around experimentation, which may involve inserting new workflows or technology to enhance efficiency.
- Control: Finally, after improvements have been implemented, this phase safeguards the gains achieved. Control charts and regular audits ensure that processes remain on track and prevent regression to old habits.
Implemented correctly, DMAIC can be a game-changer, resulting in significant cost savings and operational excellence.
"A well-defined problem is halfway to being solved."
DMADV Framework
While DMAIC is about improving existing processes, DMADVāDefine, Measure, Analyze, Design, and Verifyāfocuses on developing new products or processes that meet specific customer needs.
- Define: Just like in DMAIC, the journey begins by defining goalsāthis time, specifically in terms of customer expectations and requirements. A tech company might want to create a new software that responds faster to user queries.
- Measure: Next, the design team assesses critical factors that affect the product's feasibility. This might include measuring technological capabilities or budget constraints akin to laying down blueprints for a skyscraper.
- Analyze: In this step, teams evaluate design alternatives concerning how well they meet the identified requirements. This may involve simulations or statistical methods to project performance outcomes.
- Design: Hereās where creativity takes center stage. The proposed designs are fleshed out, and prototypes developed. Teams may rely on feedback loops from potential users to refine their creations.
- Verify: Finally, the new design is rigorously tested and verified. This phase is critical, as it determines whether the new product or process meets the intended goals and customer satisfaction before full-scale implementation.
Each methodology addresses unique project requirements, thus making them indispensable for any organization serious about quality and efficiency in their operations.
Roles within Six Sigma Projects
Understanding the dynamics of roles within Six Sigma projects is crucial for their successful implementation. Six Sigma is not just a set of tools; it is a philosophy that necessitates a cultural shift within an organization. The structure of the team plays a vital role in how effectively the principles of Six Sigma are applied. Having clear roles and responsibilities facilitates smoother project execution and better outcomes. This clarity fosters accountability and enhances collaboration amongst team members, which is essential for improving processes and achieving project goals.
Team Structure and Roles
The team involved in a Six Sigma project is typically composed of various roles, each with distinct responsibilities. Hereās a breakdown of the common roles:
- Project Sponsor: Usually a high-ranking member of the organization, they provide support, resources, and oversight for the project. Their backing is crucial for aligning the project's objectives with business goals.
- Champion: This individual helps bridge communication between the project team and executive management. They ensure the project aligns with organizational strategy and assists in removing obstacles that may hinder progress.
- Master Black Belt: The go-to expert on Six Sigma methodologies, they train and mentor both Black Belts and Green Belts. Master Black Belts guide the project team towards methodological sound practices and provide advanced statistical support.
- Black Belt: Responsible for project execution, Black Belts are full-time Six Sigma project leaders. They analyze data, manage project timelines, and serve as the primary point of contact for project updates.
- Green Belt: Working under Black Belts, Green Belts typically handle data collection and analysis on a part-time basis while still fulfilling their other job responsibilities. Their participation is essential in gathering meaningful insights for the project.
- Team Members: These individuals, who may be from various functions within the organization, contribute their specific expertise and skills to support project objectives. They are essential for implementing changes and sustaining improvements.
A structured, well-defined team not only sets the project up for success but also encourages a collective approach to problem-solving.
Champion and Master Black Belt
The relationship between the Champion and the Master Black Belt is fundamental in steering Six Sigma projects. The Champion is the driving force behind a project, vested in its success at a strategic level, while the Master Black Belt functions as the projectās technical expert and mentor.
- Champion: Their role is pivotal as they secure buy-in from top management and motivate team members. Champions need to be influential and possess strong communication skills to articulate the vision and importance of Six Sigma initiatives throughout the organization. They act as advocates who ensure the project's alignment with business strategy and help in resource allocation.
"The effectiveness of Six Sigma projects can often hinge on the visibility and commitment provided by Champions within an organization."
- Master Black Belt: With a deeper level of expertise, Master Black Belts take responsibility for ensuring that projects follow rigorous methodologies. They facilitate training sessions, ensuring that understanding of Six Sigma principles permeates the organization. Their mentorship helps nurture emerging talent in the Six Sigma community while also fortifying the technical aspects needed for project success.
In essence, these two roles are like the gears in a well-oiled machine; their collaboration enhances problem-solving capabilities and ensures that the Six Sigma projects not only start strong but finish stronger, driving long-term improvements.
Tools and Techniques in Six Sigma
In Six Sigma projects, tools and techniques play a crucial role in ensuring that objectives are met efficiently and effectively. They provide a structured approach that guides teams through every phase of the project. Without these tools, the process can become mired in confusion, leading to miscommunication and wasted resources.
The effectiveness of Six Sigma largely hinges on its data-driven nature, which necessitates the use of various tools for analysis, measurement, and implementation. Understanding which tools to utilize, and how to effectively apply them, can make a significant difference in the success of a project. Key benefits include:
- Enhanced Accuracy: Statistical tools minimize human error, leading to more reliable data.
- Streamlined Processes: Techniques such as process mapping help visualize workflows, revealing inefficiencies and bottlenecks.
- Root Cause Identification: Understanding the underlying issues in a process not only fixes current problems but also prevents future ones.
Statistical Tools
Statistical tools are at the heart of Six Sigma methodologies. They help quantify data, identify trends, and make informed decisions based on statistical analysis. Common examples include:
- Control Charts: These tools monitor process variation over time, ensuring that the process operates within established limits.
- Hypothesis Testing: This helps determine if the observed effects in the data are statistically significant.
- Regression Analysis: It identifies relationships between variables, enabling predictions based on input changes.
Using these tools effectively can aid teams in distinguishing between common cause variation and special cause variation, allowing for targeted improvements.
Process Mapping
Process mapping serves as a visual representation of the workflow in a given process. By outlining each step in a process, teams can identify not just where issues lie but also how to effectively address them. A well-crafted process map can:
- Highlight Inefficiencies: Visualizing the flow can shine a light on redundancies and delays.
- Facilitate Communication: Everyone involved gains a clear understanding of their contributions and responsibilities.
- Serve as a Reference: A documented process map can be referred to in future analysis, ensuring consistency.
Engaging in process mapping is akin to navigating with a GPS; it helps in avoiding roadblocks and sticking to the best route towards achieving project goals.
Root Cause Analysis
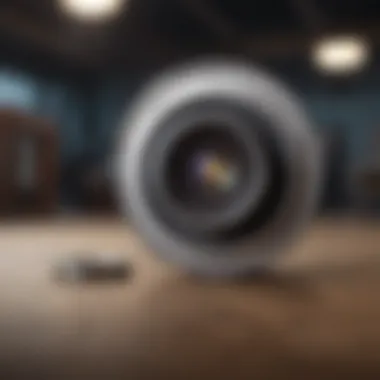
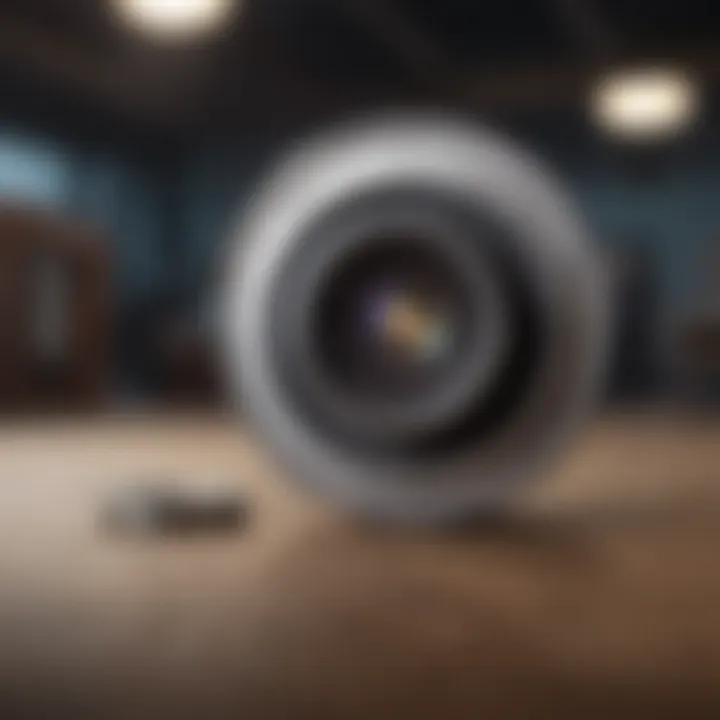
Root cause analysis is a technique that dives deep into the issues affecting process performance. It focuses on identifying the fundamental causes of problems rather than merely addressing superficial symptoms. Common methods utilized include:
- Fishbone Diagrams: Also known as Ishikawa diagrams, they visually outline potential causes contributing to an issue, categorized by type.
- 5 Whys: This method involves asking "why" repeatedly until the root cause is identified. Itās simple yet effectively gets to the heart of the matter.
- Pareto Analysis: This tool leverages the 80/20 rule, prioritizing problems based on their impact to focus efforts where they will make the most difference.
By addressing root causes, organizations can enact sustainable solutions that lead to lasting improvements. This not only enhances performance but also fosters a culture of accountability and continuous improvement.
Remember, understanding and applying the right tools and techniques within Six Sigma can lead to measurable improvements and a marked increase in organizational efficiency.
Measuring Success
Measuring success within the framework of Six Sigma projects is not merely a checklist activity; it is the backbone that influences every strategic decision made throughout the project lifecycle. Understanding how to assess success extends beyond simple metrics; it encompasses discerning the long-term benefits and implications for the organization as a whole. An effective measurement is pivotal for validating the improvements made during the project, ensuring that resources are allocated appropriately, and guiding future initiatives. The significance of this process cannot be understated; it shapes the narrative of continual improvement and informs stakeholders of the tangible value generated.
Key Performance Indicators (KPIs)
KPIs serve as the navigational compass in Six Sigma projectsāwithout them, one might feel adrift in a sea of data. These indicators offer concrete measures to evaluate the effectiveness of efforts in enhancing process efficiency and quality. When selecting KPIs, itās crucial to define metrics that align not only with project goals but also with broader organizational objectives. Common KPIs might include cycle time reduction, defect rates, or customer satisfaction levels.
- Cycle Time Reduction: Measures the time taken to complete a process, providing insights into operational efficiency.
- Defect Rates: Quantifies the number of defects per unit of production, directly impacting quality control.
- Customer Satisfaction Levels: Assesses how well the organization meets customer expectations, influencing retention and loyalty.
Incorporating these key indicators allows teams to maintain a laser-sharp focus on critical areas while simultaneously raising the stakes for performance accountability. The data gleaned from KPIs provides a basis for informed decision-making and can help pivot strategies in real-time if things stray off course.
"If you canāt measure it, you canāt improve it." - Peter Drucker
Return on Investment Analysis
Return on Investment (ROI) analysis is the lens through which the financial benefits of Six Sigma projects can be examined. This analysis offers stakeholders a clear picture of how much value is being created versus the investment made, facilitating an informed dialogue about project viability. To conduct a thorough ROI analysis in the context of Six Sigma, several factors should be taken into account:
- Initial Investment: This includes costs related to training, tools, and time spent by team members.
- Savings Generated: Helps to quantify the savings stemming from reduced waste, improved processes, or enhanced quality.
- Timeframe for Returns: Itās important to establish how quickly the benefits will manifest; a quick return can often justify a project that may appear costly upfront.
The formula for calculating ROI is straightforward:
This serves as a powerful narrative when presenting project outcomes to executives or external stakeholders. A well-articulated ROI analysis can turn skeptics into advocates, underscoring the importance of data-driven decision-making in bolstering corporate interest and viability in Six Sigma initiatives.
By delving into KPIs and ROI analysis, organizations can unveil success grounded in observable and quantifiable metrics, expanding the embrace of Six Sigma principles within their operational spectrum.
Challenges in Implementing Six Sigma Projects
In the realm of Six Sigma, while the methodology guarantees a structured approach for enhancing quality and efficiency, there are hurdles that organizations must navigate. Understanding these challenges is paramount for success. Resistance to change, data quality issues, and sustaining improvements are among the most significant impediments that can impede the effectiveness of Six Sigma initiatives. Each of these elements can act as a double-edged sword, where, if not adequately addressed, they can lead to project stagnation or even failure.
Resistance to Change
Change is often met with a mix of skepticism and apprehension. Employees who have been doing things a certain way for years may feel threatened by new processes. This resistance to change can stem from a variety of factors, including fear of the unknown or lack of trust in managementās motives. In essence, when people feel their routines are at stake, a natural defense mechanism kicks in. To mitigate such resistance, organizations must foster a culture that embraces change.
One approach involves involving team members from the outset. When employees are part of the decision-making process, they often become champions for the change. Instead of sidelining their concerns, addressing them head-on can help alleviate tensions. For example, providing education about Six Sigmaās benefits through workshops or training can not only inform but also empower the workforce.
"Change is the only constant in life." ā Heraclitus
By establishing open communication regarding intentions, expectations, and the anticipated outcomes, management can slowly shift the mindset of the team.
Data Quality Issues
At the heart of Six Sigma lies a strong emphasis on data. However, data quality issues can derail projects faster than one might assume. When the data being analyzed is flawedāeither due to inaccuracies, inconsistencies, or lack of accessibilityāthe results will invariably lead to misguided conclusions.
To ensure the integrity of data, organizations must prioritize robust data management practices. This involves regular audits and implementing standard operating procedures for data collection and analysis. Training personnel on how to accurately input data is equally essential. Beyond just collecting data, the context in which it is gathered matters too. For instance, a manufacturing plant may find that variations in ambient temperature during production impact product quality. Recognizing and documenting such environmental factors can vastly improve the reliability of the data being utilized.
Sustaining Improvements
After implementing change, the real challenge lies in sustaining improvements. Many organizations experience a phenomenon known as 'improvement fatigue.' This occurs when early successes lead to complacency. To combat this, itās crucial to establish mechanisms for ongoing assessment and refinement.
This means not only monitoring Key Performance Indicators but also fostering a mindset of continuous improvement. Documentation of processes, coupled with regular feedback sessions, can keep the team engaged and focused. Having a dedicated team to oversee these initiatives can create accountability, ensuring that the gains made aren't just temporary spikes but part of a long-term strategy.
Real-World Applications
The realm of Six Sigma has transcended its origins in manufacturing to profoundly influence a variety of sectors. The significance of understanding real-world applications cannot be overstated because it provides insight into how theoretical frameworks translate into practical benefits. By learning from actual implementations, organizations can glean valuable lessons that shape their strategies. The essence of Six Sigma lies in its ability to minimize waste and enhance quality, which can lead to substantial cost savings and operational efficiencies.
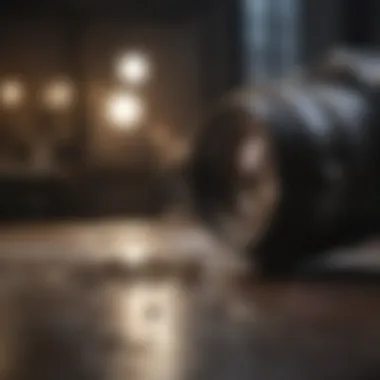
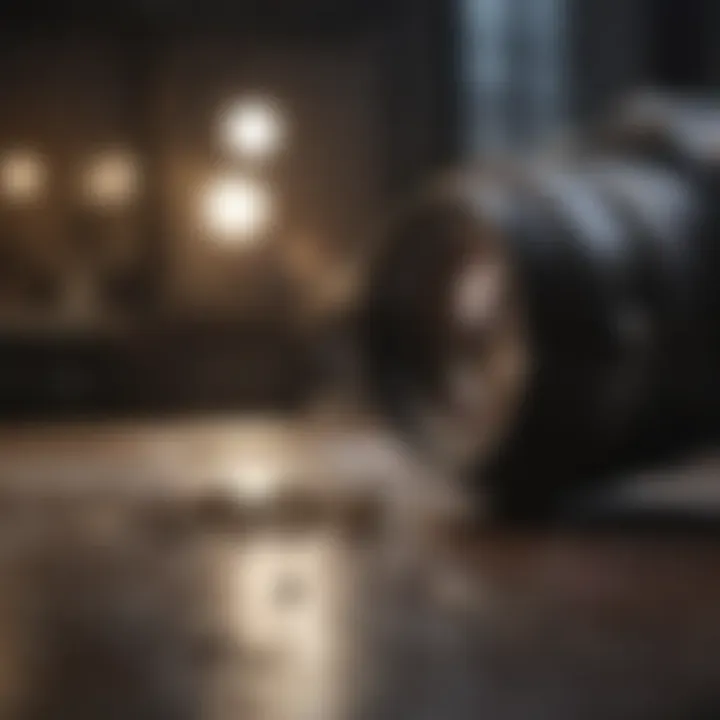
Manufacturing Industry
In manufacturing, Six Sigma is often employed as a catalyst for quality improvement. The approach is not merely about rectifying defects; itās about embedding a culture of continuous improvement. For example, a company like General Electric, renowned for its Six Sigma initiatives, utilized the methodology to reduce manufacturing defects, which in turn saved billions of dollars.
Implementing Six Sigma in manufacturing can include:
- Standardization of Processes: Establishing uniform procedures ensures consistency across the production line, which aids in maintaining quality.
- Enhanced Training and Development: Workers are trained to identify issues in real time, fostering a proactive rather than a reactive approach.
- Waste Reduction: By analyzing data, manufacturers can pinpoint inefficiencies and address them systematically.
The tangible benefits often manifest as improved product quality, reduced cycle times, and heightened customer satisfaction. Moreover, manufacturers observing Six Sigma principles frequently report higher profitability, showcasing the financial impact of these methods.
Service Sector Impacts
The service sector has seen an uptick in Six Sigma applications, driven by its focus on customer satisfaction and process efficiency. Companies in hospitality, healthcare, and finance have adopted Six Sigma to refine their service delivery.
One illustrative example lies in the healthcare industry. Hospitals applying Six Sigma have significantly decreased patient wait times and improved care quality. Techniques such as process mapping and statistical analysis empower healthcare professionals to streamline operations. Key elements and benefits in the service sector include:
- Customer Focus: By applying Six Sigma, organizations gain insights into customer behavior and satisfaction, tailoring their services accordingly.
- Efficiency in Operations: Data-driven methods help in identifying bottlenecks, leading to swifter service delivery and reduced operational costs.
- Strategic Decision Making: The availability of precise data allows management to make informed decisions, ultimately leading to better outcomes for both the organization and its clients.
As companies in the service sector continue to embrace these methodologies, they demonstrate a commitment to quality and efficiency that resonates with modern consumers, ensuring sustained growth and competitive advantage.
"Six Sigma is not just a methodology; itās a commitment to continual improvement and customer satisfaction that reverberates through every aspect of a business."
Comparative Analysis
The section on Comparative Analysis stands as a critical part of understanding the landscape of Six Sigma projects. This part provides insight into how Six Sigma stacks up against other methodologies, highlighting its particular strengths and weaknesses. This comparative approach allows organizations to make informed decisions that align with their goals, resources, and unique challenges. In today's fast-paced business world, discernment between varied efficacy approaches can mean the difference between project success and costly failure.
By examining different methodologies, companies can better appreciate the nuances of Six Sigma, understanding when it shines and when alternative approaches might serve better. Itās about finding the right tool for the job, tailored to both organizational culture and project objectives. Cross-analysis also fosters a mindset of continuous improvement through learning from others' experiences, thus broadening the horizons of possible solutions.
Six Sigma vs. Other Methodologies
When discussing Six Sigma in comparison to other methodologies, it becomes evident that each strategy comes with its unique flavor. While some lean towards efficiency, others may emphasize creativity, speed, or cost outage reductions. Consider Total Quality Management (TQM), which shares a foundational principle with Six Sigma but often lacks the data-driven approach that defines the latter.
Six Sigma thrives on quantitative measurement, leaning on statistical tools and quality control processes. This approach is particularly valuable in industries where precision is paramount, such as manufacturing and healthcare. By contrast, methodologies such as Agile prioritize flexibility and rapid iteration over statistical rigor. Agile is excellent for software development but may not adequately tackle quality in complex manufacturing scenarios. Hereās a quick look at the two:
- Six Sigma: Data-driven, focuses on defects and variation.
- Total Quality Management: More holistic, emphasizes continuous quality improvements.
- Agile: Adaptative, focuses on speed and change responsiveness, sometimes at the cost of streamlined quality control.
"In every comparison, there is an opportunity to learn, whether itās adapting a new approach or enriching an existing one."
Ultimately, aligning method with task can optimize outcomes significantly. A thorough understanding of each methodology provides a roadmap for selecting the right strategy depending on project demands.
Lean vs. Six Sigma
Lean methodology, known for its focus on waste elimination and efficiency, complements Six Sigma but differs in scope. While Lean pursues speed by trimming unnecessary steps, Six Sigma analyzes variations and aims for defect-free processes. In various ways, they serve different ends of the spectrum:
- Lean: Prioritizes speed and reducing waste in processes, sustaining continuous flow.
- Six Sigma: Centers on error reduction through statistical analysis.
This partnership between Lean and Six Sigma is popularly referred to as Lean Six Sigma. Organizations aiming for overall efficiency often blend these methodologies, creating a hybrid model that reduces waste while improving quality.
While Lean might cut down on unproductive time, when assessed with Six Sigma, the focus shifts to creating value without sacrificing quality. So, when organizations look to adopt either or both methodologies, they must first assess currently existing pain points in processes to determine the most fitting strategy.
By navigating this comparative analysis of Six Sigma and its methodologies, businesses not only refine their operational strategies but also fuel their journey toward impactful continuous improvement.
Future Trends in Six Sigma
In today's rapidly evolving business environment, staying ahead of the curve is essential. Future trends in Six Sigma reflect the changing landscapes of industries and technologies, highlighting the increasing need for adaptability and innovation. By understanding these trends, organizations can better align their Six Sigma initiatives with contemporary business demands.
Integration with Agile Practices
The integration of Six Sigma with Agile practices represents a shift in both methodology and mindset. Businesses increasingly require flexibility to respond to market changes swiftly. Agileās iterative approach, characterized by quick cycles and continuous feedback, complements the structured data-driven focus of Six Sigma.
Benefits of this Integration:
- Enhanced Responsiveness: Agile's adaptability allows teams to pivot based on real-time data insights. This is crucial in tapping into customer needs and adjusting processes accordingly.
- Increased Collaboration: Agile emphasizes team interactions, creating a culture where suggestions and ideas freely circulate. This enhancement fosters communication, making it easier for team members to initiate Six Sigma projects relevant to customer demands.
- Faster Time to Value: Combining the two methods leads to quicker project execution. Instead of waiting for long-term analysis results, Agile practices allow teams to implement improvements sooner while continuously refining processes based on Six Sigma metrics.
Digital Transformation
As industries embrace digital transformation, the relevance of Six Sigma grows. The infusion of technology into processes aids in streamlining workflows and enhancing data collection and analysis.
Consider these aspects of digital transformation in the context of Six Sigma:
- Data Availability and Quality: With advanced analytics tools, organizations now have access to enormous amounts of data. Six Sigma techniques become invaluable in interpreting this data, ensuring that decisions are not just instinctual but grounded in statistical evidence.
- Automation and Efficiency: Automation technologies can minimize human error and enhance process efficiency. Six Sigma methodologies facilitate identifying areas ripe for automation, thus reinforcing overall productivity.
- Real-Time Feedback: Enhancements in technology allow for continuous monitoring of processes. Real-time insights lead to immediate corrective actions, which strengthens Six Sigma's core principle of ongoing improvement.
"Integrating Six Sigma with digital tools offers a pathway to not just survive but thrive in this digital age, marking an evolution in how we understand operational excellence."